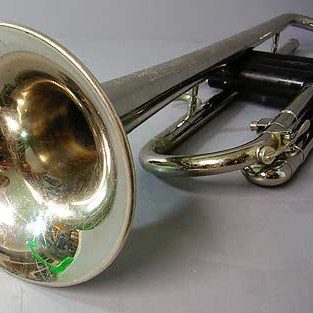
The Reynolds Ranger trumpet was produced at Olds' Fullerton plant from 1971-75 and was identical to the Olds Pinto model. The Ranger/Pinto model featured a modular design that allowed the entire horn to be disassembled into component parts, including interchangeable valves whereby any piston could be inserted into any of the valves and work properly. The intent behind this design was to allow for easier repair of student damage - the modular design allowed specific parts to be replaced on the horn more rapidly than actually repairing the damage.
1971-1975
F.A. Reynolds (Fullerton, Calif.)
Designed specifically for the player just starting out. Free-blowing features give the student easier and more complete control over each note, while the lead pipe is precisely contoured for just the right amount of resistance for effective development of embouchure and breath support. The straight through valve design which makes open tones smooth and natural is usually only found in expensive, professional models. The valve cluster is made of virtually damage proof Valox™. The valves are positioned slightly closer together than standard models to accommodate a smaller hand. The weight is perfectly distributed throughout the horn. Supplied in a durable case with accessories.
NOTES
Former Olds plant worker Chuck Madere described the production and marketing of the Olds Pinto valve design in his article, Working at F.E. Olds 1962-1972 (source: Olds Central):
"One day they gave us a new design piston to make that had no 1,2 or 3. One piston would fit all three valves. It was interchangeable and was not stamped with a number. This would be the Pinto trumpet. Not only were the valves interchangeable but also the braces would unscrew and the bell and leadpipe would come off without unsoldering. In order to make the valves that way they had to change the position of the holes in the piston. This made a problem for us. The top and middle holes through the piston were too close together but they had to be that way to make the valves interchangeable. When balling out (expanding the tubing on the balling machine) there was a big hump in the bottom of the top crook. It looked awful but there was no way to get around it. You had to push so hard the piston would bend or the crook would split. We had to throw away up to half of the pistons we made for this horn. The ones that were bent had to be junked, however we could save some of the tubing splits by soldering them. We hated to make these pistons. They were the hardest to make. Also when we repaired them it was always on no bonus time. Any repair time was straight time. It was a big problem that they could never get around. So here is what they did."
"I picked up an Olds brochure at the music store about the Pinto and was surprised to see they had highlighted the large bump in the top crock. Why would they do that I wondered when they tried everything they could to get rid of it. They gave it a name. They called it "turbotron". The brochure said the horn played so well because the "turbotron" compressed the airflow then forced it out at increase speed and therefore improved the sound. It was a brilliant concept to take a problem and turn it into a plus. The Pintos did not do very well and we did not make many of them."
The purpose of this website is to preserve the history of the F. A. Reynolds Company and the distinctive qualities of its brass instruments. Contempora Corner and contemporacorner.com are not related or associated in any way to the former or current F.A. Reynolds Company.
Copyright © 2004-2024 ElShaddai Edwards. All Rights Reserved. Terms of Use.